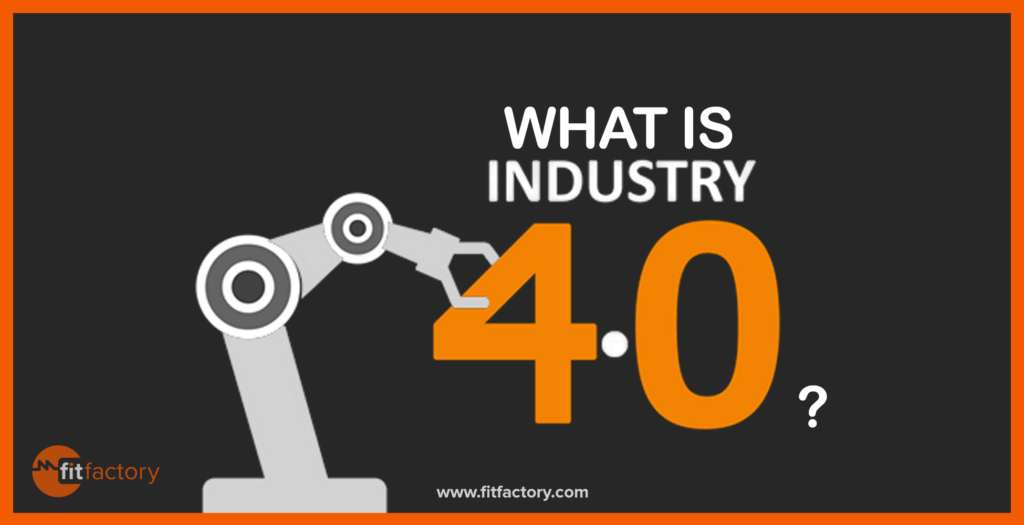
What is Industry 4.0?
Industry 4.0 is the next revolution in industrialization, or as many are calling it ‘the Fourth Industrial Revolution’, and is the current trend of automation and data exchange in manufacturing technologies. But what is Industry 4.0? What does it mean? What are the main challenges? And what can it do for your business? Let’s find out.
Building ‘The Smart Factory’
The aim for industry 4.0 is to create ‘smart factories’ that utilise automated computing algorithms to monitor physical processes, and make decentralized decisions. Once these factories have evolved into smart factories they will have the capabilities to self-manage any issues and internal processes.
So that’s the aim, but the way that Manufacturing and Production sectors are developing to that automated state is by integrating various advances in technology, including:
- Cloud Computing – Internet hosted computing that allows remote access to apps, services and stored data
- The Internet of Things – Uses the cloud to store and automate processes in objects synced to the internet such as; internet enabled automobiles or remote home lighting systems.
- Data Integration – The combination of technical and business processes used to combine data from disparate sources into meaningful and valuable information.
Both cloud computing and the Internet of Things are relocating manual processes (normally managed internally in businesses by real people and machines) into the cloud where they can be managed from anywhere in the world. Thanks to advances in data integration, cyber physical systems can communicate with each other over the internet of things, in real time, to offer internal and cross-organizational services to all participants of the value chain. Overall, this is leading to the development of decentralised decisions in the factory.
Developing decentralised decisions
Currently, the systems are not interconnected, with one system having the entire overview, and each part of the process only having information about the process they are working on. This ensures that each part can do its job well, but restricts the possibility to use specialist expertise to innovate a better solution, as they have no idea if it will work in the overall project.
However, Industry 4.0 is ready to challenge this and revolutionize the way factories work. By taking all the individual processes that machines perform and importing them into the cloud, the workflow, management systems and overall upkeep can be done remotely. With everyone involved in the process now having access to the full plans, a decentralized system is created that opens opportunities for the improvement of sections with the end goal in mind. Therefore, manufacturing systems at every level need to be improved and evolved or your company might just get left behind.
The history of the Fourth Industrial Revolution
The term ‘industrie 4.0’ originates from a high-tech strategy project carried out by the German government to promote the computerization of manufacturing. Since forming at the world’s biggest industrial fair ‘Hannover Messe’, Industry 4.0 has been creeping up on the manufacturing sector. Not only has it advanced Germany’s engineering but it’s taking the world’s manufacturing sector along with it.
However, everyone is giving Industry 4.0 another title, the Fourth Industrial Revolution, and there is a reason for this. It has the potential to disrupt the industry just like the past three revolutions have.
- The first industrial revolution was to mobilise the mechanization of production using water and steam power.
- Followed by the introduction of mass production with the help of electrical power in the second industrial revolution.
- The third saw the digital revolution and the use of electronics and IT to further automate production.
There has been much speculation and criticism as to whether Industry 4.0 deserves the title of the fourth revolution. Many say its meaningless because technological innovation is always developing and is continuous so therefore the concept of a revolution in technology innovation is based on the lack of knowledge and details. However, Industry 4.0 differs from the past 3 industry revolutions because it’s been a long time coming and has been in talks for years. The reason it’s taking so long to hit is to allow manufacturing organisations to get ahead of the game before industry 4.0 takes over. Germany currently leads the development race with greater investment in research than all the English divisions put together, but the rest of the world is starting to catch up.
Perhaps the main difference to the 3rd industrial revolution, is the opportunity for mass customisation of products. This automation technology works through the introduction of self-optimisation, self-configuration, self-diagnosis, cognition, and intelligent support of workers. With greater flexibility throughout the production line, customers (be they business or consumer) will be able to order and receive exactly what they need. Initiatives are already underway to increase the application of these new technologies, including:
- European Commission’s International Horizon 2020 research project ‘CREMA’
- BMBF leading-edge cluster ‘intelligent technical systems’
- BMBF project RES-COM
- Cluster of excellence ‘integrative production technology for high-wage countries’
More projects are set to begin as Industry 4.0 is set to become the mainstream of modern manufacturing.
What challenges arise with Industry 4.0?
Although Industry 4.0 is an exciting breakthrough for the manufacturing industry, there are many challenges to mass implementation, including:
- Knowledge
- Culture for change
- Cost
Knowledge
One of the first things companies will need to consider is whether they have the correct knowledge to keep up with the fast-moving evolution into Industry 4.0. Not only do they need to understand everything that’s available, but they need to know which aspects are most important to implement first, and have a strategy for success. Once they have an Industry 4.0 strategy, businesses need to know how to operationalise Industry 4.0 to fully enhance their systems. It’s not just about the MD understanding the applications, companies will need to train staff or hire new staff with the right skill set to optimise Industry 4.0 in their business.
Culture for change
In any business, change on the scale that is needed will always meet resistance, and Manufacturing companies are no different. It is essential though that key decision makers and influencers in the business are on board, aware of the need for change, and are fully committed to driving it forwards. Companies will have to re-evaluate everything, including the way suppliers, engineers and analysts work. Reliability and stability will be critical for machine-to-machine communication and being together as a team will be essential when diving into the new movement.
Cost
Another key challenge, is cost. With so many new technologies on the horizon, it is likely to require huge investment to implement these new technologies. To maximise benefits, companies won’t be able to purchase just one new system or implement one new process, in some cases, it can require renovation of the entire production line. Of course, as more new technologies are developed and more widely used, low cost alternatives are also becoming available. However, this does not change the fact that companies will need to invest money in plant, people and processes to ensure they actualise a beneficial Industry 4.0 strategy.
What advantages will we gain from it?
However, for all the challenges that Industry 4.0 produces, there are even greater benefits on offer, including:
- Automated data analysis
- Streamlined processes
- Lower production costs
- Lean operations
- Easier compliance with accreditations & standards
- More business opportunities
- Fewer risks
To name just a few.
Data
One big benefit that will come from it is the generation, analysis and use of data. Data is available on every aspect of a manufacturing company: the people, plant, process, product and partners. Data providers can provide worthwhile information about different aspects of the factory and if we manage that correctly, big benefits can be gained to improve productivity and generate continuous sustainable improvements in all business areas.
Improved productivity
With continuously increasing demand in the manufacturing sector, having greater efficiency, flexibility and sustainability in your factory is more important than ever. The basic principle of industry 4.0 is that by connecting machines and systems, businesses are creating intelligent networks along the value chain to control each other autonomously. For example, machines can predict failures and trigger maintenance processes automatically instead of maintenance having to be done manually. This ensure that issues are proactively detected and prevented, rather than risking the possibility of machine downtime that leads to low productivity and potentially missing deadlines.
On a larger scale, machines will help make the factory leaner, with automated push/pull or Kanban systems, and streamline manual processes, allowing more time for employees to analyse and improve current performance.
Not only will the benefits be for companies but of course, the customers will gain great benefits from this movement also. With the automating processes now being more reliable, customers are already seeing the benefits such as better quality and more consistent products but in the future, further improvements such as personalisation will be brought into the mix without the heavy costs that are associated with such things now.
It is highly likely that over time, the production world will become more and more networked until everything is interlinked with everything and therefore the complexity of production and supplier networks will grow large and quickly. All networks and processes have so far been limited to one factory but now with Industry 4.0 fast approaching, these individual boundaries won’t exist and all factories will be interconnected.
Where are we today?
Many businesses are claiming it’s difficult to keep up with the industrial revolutions. However, many of the larger organisations, such as Bosch and KPMG are already seeing huge benefits from restructuring of their factories, and in the next few years, European industrial companies look set to invest 140 billion euros, annually, in industrial internet applications. And the new technologies are being applied in almost every area:
- Services and Business Models
- Reliability and Continuous Productivity
- IT Security
- Machine Safety
- Product Lifecycles
- Industry Value Chain
- Workers’ Education and Skills
- Socio Economic Factors
- Industry Demonstration
However, while many manufacturers are already thinking about and implementing their digital transformation strategy, there similar amount of businesses refusing to admit Industry 4.0 is even happening. The fourth revolution isn’t something that will jump into our systems overnight, and it requires everyone to get on board to realise its potential, so we need to act and start our transformation before the country is left behind.
At Fitfactory, we’re making Industry 4.0 simple and easy to use for manufacturing SMEs. Supporting more than 400 SMEs to embrace Industry 4.0 and realise ROI from their digital transformation, we see the tangible benefits of Industry 4.0 adoption everyday.
Get in touch to find out how you can start your digital transformation.